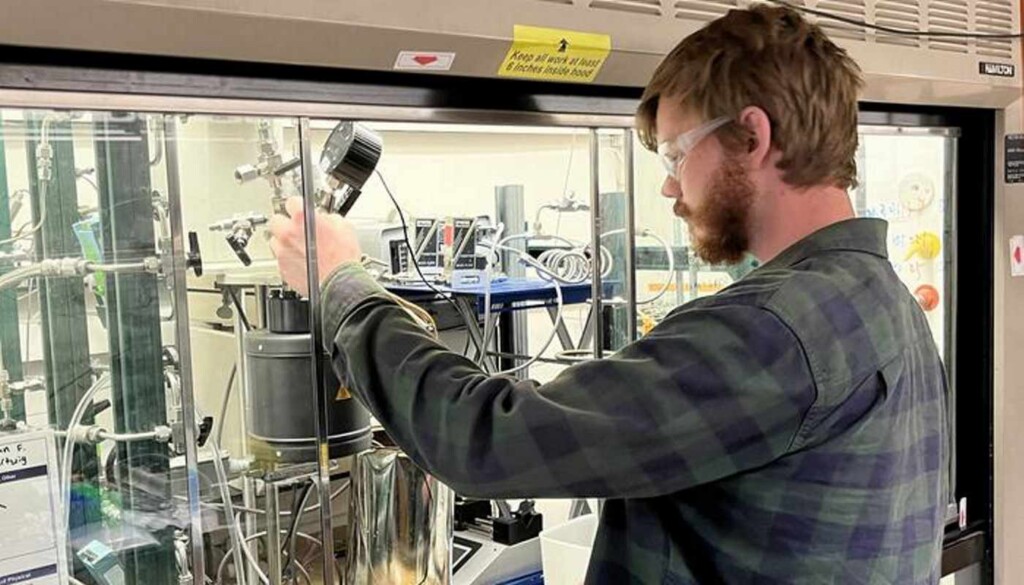
An innovative chemical procedure turns ubiquitous waste plastic items in our society into hydrocarbon building blocks for use in making new plastics.
The scientists behind the project explained that the process works “equally well” with the two dominant types of consumer plastic waste: polyethylene, the component of most single-use plastic bags; and polypropylene, the stuff of hard plastics, from microwavable dishes to luggage—which together are called polyolefins.
It also efficiently degrades a mix of the two types of plastics, according to the findings published in the journal Science.
The research team says the catalytic process, developed at Lawrence Berkeley National Laboratory, could help bring about a circular economy for many throwaway plastics, with the plastic waste converted back into the monomers used to make polymers, thereby reducing the fossil fuels used in making virgin plastic.
“We have an enormous amount of polyethylene and polypropylene in everyday objects, from lunch bags to laundry soap bottles to milk jugs—so much of what’s around us is made of these polyolefins,” said research leader Professor John Hartwig, of University of California, Berkeley.
Hartwig and his collaborators in a public sector-academia partnership developed a chemical process that employed three different bespoke heavy metal catalysts: one to add a carbon-carbon double bond to the polyethylene polymer and the other two to break the chain at this double bond and repeatedly snip off a carbon atom. However, the catalysts broke down in the liquid reaction and were rarely recoverable, making the process difficult to scale.
That was two years ago. Today, as part of a new process, the expensive, soluble metal catalysts have been replaced by cheaper solid ones commonly used in the chemical industry for continuous flow processes that reuse the catalyst, including sodium on alumina, and tungsten oxide on silica.
“You can’t get much cheaper than sodium,” Hartwig said, “and tungsten is an earth-abundant metal used in the chemical industry in large scale, as opposed to our ruthenium metal catalysts that were more sensitive and more expensive.”
THINK PLASTIC WASTE IS WITH US FOREVER?
- There’s a Surprisingly Easy Way to Remove Microplastics From Drinking Water: Boil it
- Revolutionary New ‘Living Plastic’ That Could Slash Damage to the Environment Developed by California Researchers
- Fishing Nets and Carpets Can Be Recycled Molecularly Thanks to Genius Chemist and Brand New Catalyst
- Plastic Waste Can Now be Turned into Soap Thanks to Eureka Moment from Virginia Tech
- Ordinary Plastic Turned into Diamonds Via Laser Beam in the Blink of An Eye
Continuous flow processes can be scaled up to handle large volumes of material, a necessary prerequisite if this is to be used widely and at scale.
Polyethylene and polypropylene plastics make up about two-thirds of consumer plastic waste worldwide. About 80% end up in landfills, incinerated, or simply dumped in the street where they degrade into microplastics to eventually enter rivers and oceans.
To reduce waste, scientists have been looking for ways to turn polyolefins into something more valuable, such as the monomers that help to produce new plastics.
Hartwig noted that while many researchers are hoping to redesign plastics from “the ground up” to be easily reused, today’s hard-to-recycle plastics will be a problem for decades.
“One can argue that we should do away with all polyethylene and polypropylene and use only new circular materials, but the world’s not going to do that for decades and decades,” he said. “Polyolefins are cheap, and they have good properties, so everybody uses them.”
SHARE What’s Going On At The Berkeley National Labs With Your Friends…