This article, by Joshua M. Pearce of Michigan Technological University, has been republished from The Conversation under a Creative Commons license.
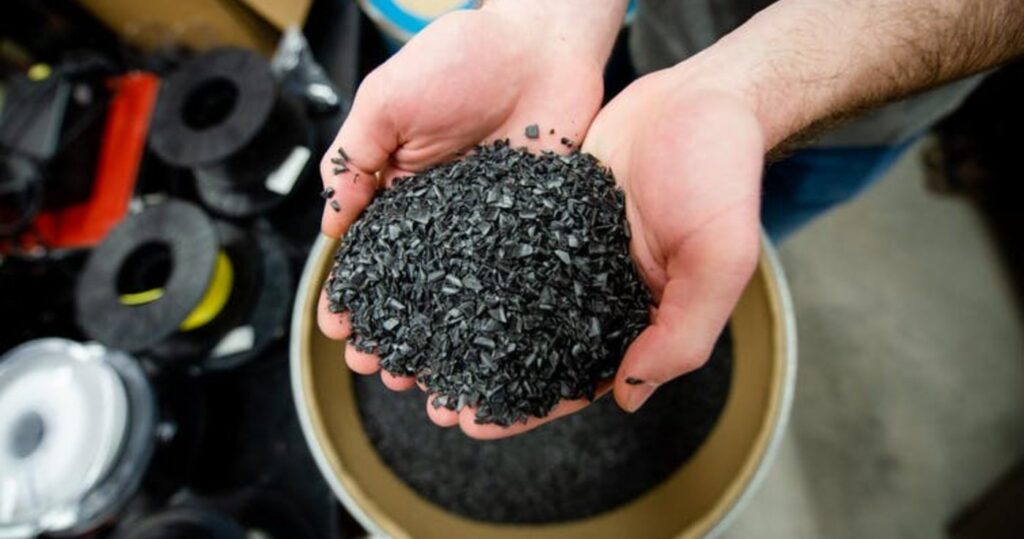
People will recycle if they can make money doing so. In places where cash is offered for cans and bottles, metal and glass recycling has been a great success. Sadly, the incentives have been weaker for recycling plastic.
But now, several technologies have matured that allow people to recycle waste plastic directly by 3D-printing it into valuable products, at a fraction of their normal cost. People are using their own recycled plastic to make decorations and gifts, home and garden products, accessories and shoes, toys and games, sporting goods and gadgets from millions of free designs.
This approach is called distributed recycling and additive manufacturing, or DRAM for short.
As a professor of materials engineering at the forefront of this technology, I can explain—and offer some ideas for what you can do to take advantage of this trend.
How DRAM works
The DRAM method starts with plastic waste—everything from used packaging to broken products.
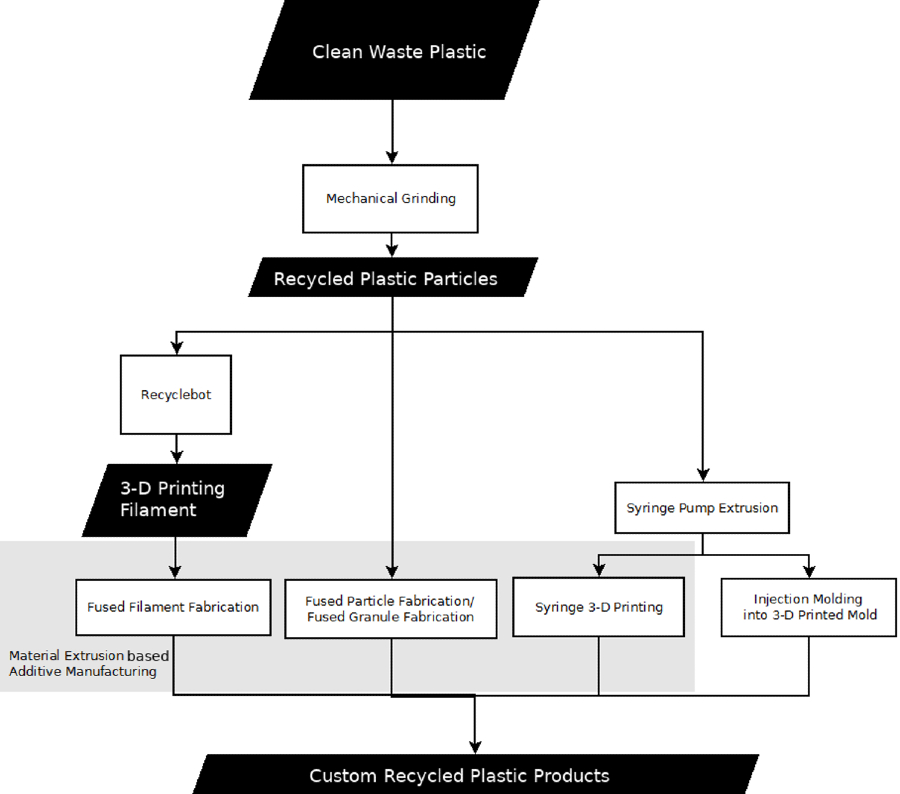
The first step is to sort and wash the plastic with soap and water or even run it through the dishwasher. Next, the plastic needs to be ground into particles. For small amounts, a cross-cut paper/CD shredder works fine. For larger amounts, open-source plans for an industrial waste plastic granulator are available online.
Next you have a few choices. You can convert the particles into 3D printer filament using a recyclebot, a device that turns ground plastic into the spaghetti-like filaments used by most low-cost 3D printers.
Filament made with a 3D-printable recyclebot is incredibly cheap, costing less than a nickel per pound as compared to commercial filament, which costs about US$10 per pound or more. With the pandemic interrupting global supply chains, making products at home from waste is even more appealing.
CHECK OUT: We Use 6 Billion Face Masks a Day—But Scientists Have a Genius Way to Turn Them Into Roads
The second approach is newer: You can skip the step of making filament and use fused particle fabrication to directly 3D-print granulated waste plastic into products. This approach is most amenable to large products on larger printers, like the commercial open source GigabotX printer, but can also be used on desktop printers.
Granulated plastic waste can also be directly printed with a syringe printer, although this is less popular because print volume is limited by the need to reloading the syringe.
My research group, along with dozens of labs and companies throughout the world, has developed a wide array of open source products that enable DRAM, including shredders, recyclebots and both fused filament and fused particle 3D printers.
These devices have been shown to work not only with the two most popular 3D printing plastics, ABS and PLA, but also a long list of plastics you likely use every day, including PET water bottles. It is now possible to convert any plastic waste with a recycling symbol on it into valuable products.
Furthermore, an “ecoprinting” initiative in Australia has demonstrated DRAM can work in isolated communities with no recycling and no power by using solar-powered systems. This makes DRAM applicable anywhere humans live, waste plastic is abundant and the Sun shines – which is just about everywhere.
Toward a circular economy
Research has shown this approach to recycling and manufacturing is not only better for the environment, but it is also highly profitable for individual users making their own products, as well as for small- and medium-sized businesses. Making your own products from open source designs simply saves you money.
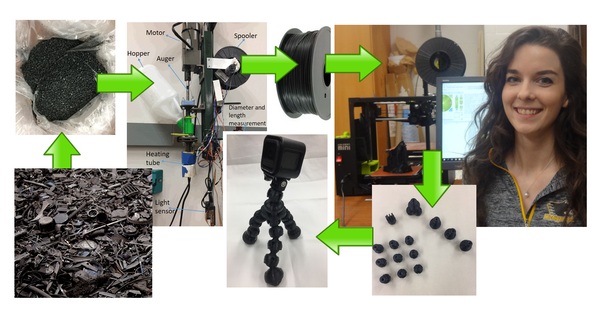
DRAM allows custom products to be made for less than the sales tax on conventional consumer products. Millions of free 3D-printable designs already exist—everything from learning aids for kids to household products to adaptive aids for arthritis sufferers. Prosumers are already 3D-printing these products, saving themselves collectively millions of dollars.
One study found MyMiniFactory users saved over $4 million in one month alone in 2017 just by making toys themselves, instead of purchasing them. Consumers can invest in a desktop 3D printer for around US$250 and earn a return on investment of over 100% by making their own products. The return on investment goes higher if they use recycled plastic. For example, using a recyclebot on waste computer plastic makes it possible to print 300 camera lens hoods for the same price as a single one on Amazon.
Individuals can also profit by 3D-printing for others. Thousands are offering their services in markets like Makexyz, 3D Hubs, Ponoko, or Print a Thing.
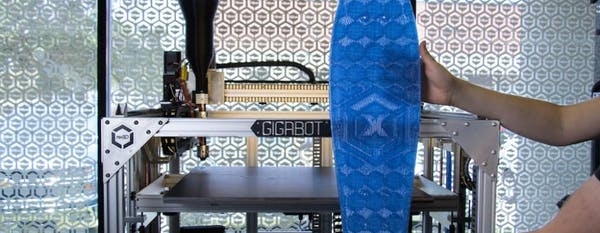
Small companies or fab labs can purchase industrial printers like the GigabotX and make returns by printing large sporting goods equipment like snowshoes, skateboard decks and kayak paddles from local waste.
Scaling up
Large companies that make plastic products already recycle their own waste. Now, with DRAM, households can too. If many people start recycling their own plastic, it will help prevent the negative impact that plastic is having on the environment. In this way DRAM may provide a path to a circular economy, but it will not be able to solve the plastic problem until it scales up with more users. Luckily we are already on our way.
Hear more about how to turn waste plastic into profit with #opensource #recycling and #3dprinting https://t.co/n2b9S4xJOa https://t.co/tpIzpQJsiA
— Joshua Pearce (@ProfPearce) October 1, 2020
3D printer filament is now listed in Amazon Basics along with other “everyday items,” which indicates plastic-based 3D printers are becoming mainstream. Most families still do not have an in-home 3D printer, let alone a reyclebot or GigabotX.
MORE: The Ever-Growing Pile of Electronic Waste is Now On the Decline, Study Finds
For DRAM to become a viable path to the circular economy, larger tools could be housed at neighborhood-level enterprises such as small local businesses, makerspaces, fabrication labs or even schools. France is already studying the creation of small businesses that would pick up plastic waste at schools to make 3D filament.
I remember saving box tops to help fund my grade school. Future students may bring leftover plastic from home (after making their own products) to help fund their schools using DRAM.
Written by Joshua M. Pearce, Wite Professor of Materials Science & Engineering, and Electrical & Computer Engineering, Michigan Technological University. Read the original article here.
DON’T WASTE the Good News—Share This Story With Pals…
So good to read a very complete article which includes exactly how this process works and the products needed to do so and where to find them. Very promising, very positive.