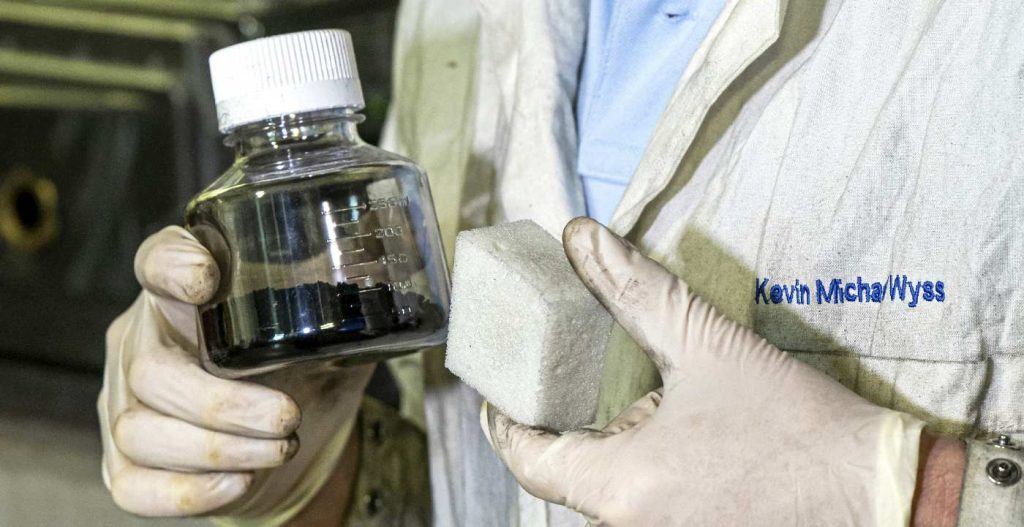
Electric cars could be made with plastic from old clunkers, according to new research.
Bumpers, carpets, mats, seating, seals, and door casings have been turned into graphene, which is the world’s lightest material.
Invented by British scientists almost two decades ago, it is set to revolutionize the automative industry.
The metal will increase vehicles’ strength while reducing weight, improving fuel efficiency, and creating rust-free paint.
It will make self-driving cars safer with sensors just one atom thick, enabling detection of obstacles even in difficult weather conditions.
The U.S. team collaborated with Ford using a state-of-the-art technique called flash Joule heating.
“Ford sent us 10 pounds of mixed plastic waste from a vehicle shredding facility,” project leader Professor James Tour, of Rice University, Houston, said. “It was muddy and wet. We flashed it, we sent the graphene back to Ford, they put it into new foam composites and it did everything it was supposed to do.
MORE: As the World Runs on Lithium, Researchers Develop Clean Method to Get It From Water
“Then they sent us the new composites and we flashed those and turned them back into graphene. It’s a great example of circular recycling.”
The recycling breakthrough could also reduce landfill waste from over 1.4 billion passenger cars used globally.
Ford has been using up to 60 lbs of polyurethane foam in its vehicles, with about 2 lbs being graphene-reinforced since 2018.
“When we got the graphene back from Rice, we incorporated it into our foam in very small quantities and saw significant improvement,” co-author Dr Alper Kiziltas, a sustainability expert at the motor giant, said. “It exceeded our expectations in providing both excellent mechanical and physical properties for our applications.”
RELATED: Scientists Powering Tesla on 9,400-mile Journey With Rolled-up Printed Solar Panels
The company first introduced it into under-the-hood components. In 2020 it added a graphene-reinforced engine cover. It’s also expected to boost hard plastics.
A new way
“Our collaborative discovery with Rice will become even more relevant as Ford transitions to electric vehicles,” co-author Dr Deborah Mielewski, also from Ford, said.
“When you take away the noise generated by the internal combustion engine, you can hear everything else in and outside the vehicle that much more clearly.”
“It’s much more critical to be able to mitigate noise. “So we desperately need foam materials that are better noise and vibration absorbers.
“This is exactly where graphene can provide amazing noise mitigation using extremely low levels.”
Graphene will also replace lithium ion batteries, currently a very heavy component of electric vehicles.
The study in Communications Engineering reused the graphene to make enhanced polyurethane for new vehicles.
Tests showed the infused foam’s tensile strength and low-frequency noise absorption increased by 34 and 25 percent, respectively, with less than 0.1 percent by weight.
And when that new car is old, the foam can be flashed into graphene again. Plastic in vehicles has increased by an estimated 75 percent in just six years.
“In Europe, cars come back to the manufacturer, which is allowed to landfill only 5% of a vehicle. That means they must recycle 95%, and it’s just overwhelming,” prof. Tour said.
The US shreds up to 15 million vehicles each year, with more than 27 million shredded globally. Much ends up being incinerated.
LOOK: This Portable EV Charger is a Game-Changer For Drivers Who Need to Plug-in
“We have hundreds of different combinations of plastic resin, filler and reinforcements on vehicles that make the materials impossible to separate,” Dr Mielewski said. “Every application has a specific loading/mixture that most economically meets the requirements.”
Engineered plastics cannot be recycled. Traditional recycling methods are expensive because they require the separation of different types.
“These aren’t recyclables like plastic bottles, so they can’t melt and reshape them,” Prof Tour explained. “So, when Ford researchers spotted our paper on flash Joule heating plastic into graphene, they reached out.”
Flash Joule heating was developed by his lab two years ago. It packs mixed ground plastic and a coke additive, for conductivity, between electrodes in a tube.
MORE: Volkswagen Gets A Lot of Buzz Premiering Their New Electric Throwback Bus – the ID. Buzz (LOOK)
The chemical cocktail is blasted with high voltage. The sudden, intense heat reaches nearly 5,000 degrees Fahrenheit vaporizing other elements, leaving behind graphene.
It offers significant environmental benefits. The process does not require solvents and uses a minimum of energy.
In experiments, the team ground shredder ‘fluff’ from end-of-life F-150 pick-up trucks without washing or pre-sorting the components.
Powder heated between 10 to 16 seconds in low current produced a highly carbonized plastic accounting for about 30 percent of the initial bulk.
The rest was outgassed or recovered as hydrocarbon-rich waxes and oils. Lead author Kevin Wyss, a graduate student, believes this could also be recycled.
The carbonized plastic was then subjected to high-current flashing, converting 85 percent of it into graphene while outgassing hydrogen, oxygen, chlorine, silicon, and trace metal impurities.
Analyses showed it produced graphene with a substantial reduction in energy, greenhouse gas emissions, and water use when compared to other methods, even including the energy required to reduce the plastic shredder fluff to powder.
Graphene was discovered in 2004 by Prof Andre Geim and Prof Kostya Novoselov at the University of Manchester. It later won them the Nobel Prize for physics.
It is tougher than diamond, but stretches like rubber. It is virtually invisible, conducts electricity and heat better than any copper wire, and weighs next to nothing.
In coming decades, the astonishing material is expected to change almost every aspect of our lives.
Transform Those News Feeds With Hopeful Stories Like This One…